Top 10 ways to improve cold chain operations
Thời sự - Logistics - Ngày đăng : 08:30, 26/08/2021
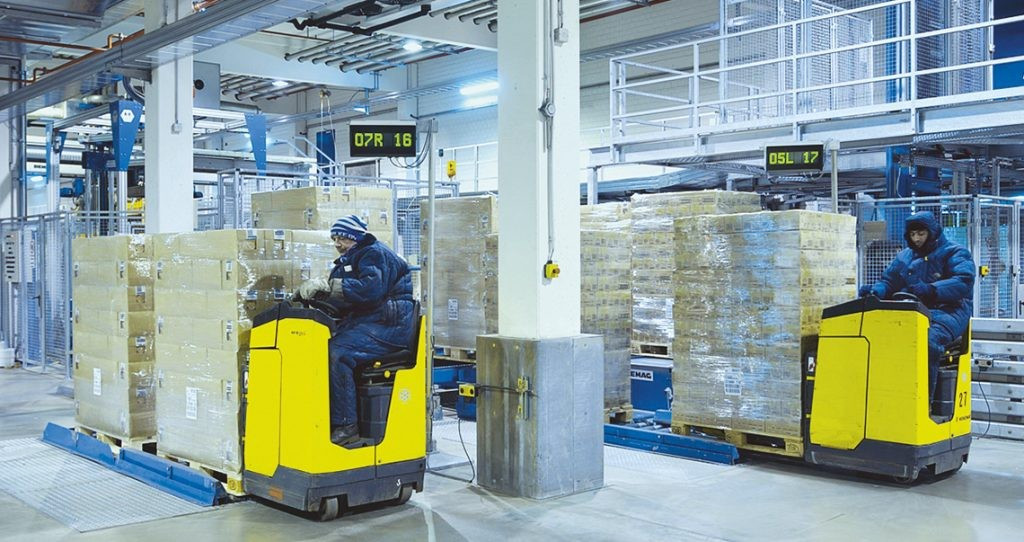
A cold chain must maintain uninterrupted refrigeration throughout storage and distribution to ensure quality
A cold chain must maintain uninterrupted refrigeration throughout storage and distribution to ensure quality. However, the problem with cold chain logistics is that they are complex, and it can be difficult to ensure proper refrigeration from loading dock to final destination. And relying on any conventional cold chain management solution that lacks the ability to monitor perishable assets in real-time is a recipe for disaster.
Recent studies reveal that 95% of respondents are not fully capitalizing on the benefits of digital supply chain technologies. Supply chain executives are eager to make the change though. The same study found that companies are looking to implement technologies like IoT, data analytics, Blockchain, and machine learning to improve their operations.
The benefits of digital cold chain logistics technologies have been proven to add big value for businesses. Leveraging digital technology, enterprises can expect increased speed to market, higher revenues, and reduced costs. A wide range of factors can impact the transport of temperature-controlled goods. Here are 10 tips to help ensure smooth cold chain operations.
1 Know your requirements
Temperature-controlled goods-whether food, vaccines, infectious substances, or other items-all have requirements that impact how they are packaged, stored, and shipped. Consider all your requirements for temperature ranges, packaging, transit time, tracking, and size and weight restrictions.
2 Understand exactly what you’re shipping
Consider the factors that can affect the type of solution needed to keep the entire shipment within the desired temperature range from origin to destination. What are the package dimensions? How much is being packed per package? Is there a single package size or multiple sizes? Knowing this information upfront will help you select optimal cold chain processes and solutions, and avoid problems later on.
3 Clearly define your goals
Do you want to save money on packaging? Reduce shipping costs? Speed fulfillment? Knowing what you’re trying to accomplish-and how you’ll measure success-will help guide the selection of cooling systems, packaging, carriers, and more.
4 Identify your pain points
Do you have trouble keeping seasonal items cold during the summer? Is sourcing or disposing of packaging difficult? What could hold up a shipment in customs? Understanding your current pain points— as well as those that may arise—will help you select solutions that align with your service, financial, and performance goals.
5 Select the right cooling systems
Determine if an active cooling system (e.g., a refrigerated truck) or a passive system (e.g., gel packs or dry ice) is best for your operation. Passive systems may be less expensive but could be higher risk if there’s a chance of delays while being transported through warm climates, or more labor intensive if they require pre- and post-conditioning.
6 Select the right cooling systems
Determine if an active cooling system (e.g., a refrigerated truck) or a passive system (e.g., gel packs or dry ice) is best for your operation. Passive systems may be less expensive but could be higher risk if there’s a chance of delays while being transported through warm climates, or more labor intensive if they require pre- and post-conditioning.
7 Play by the rules
A wide range of regulations impacts how you pack, store, and ship temperature-controlled goods. Know which rules apply to what you’re shipping and take steps to ensure all stakeholders are properly trained and adhere to these rules.
8 Pick easy-touse monitoring solutions
Companies nowadays increasingly use devices to track shipments and monitor time and temperature in real time. Chemical strip indicators are simple to use, inexpensive, and do not employ hazardous materials, such as lithium batteries, which may require additional packaging and labeling.
9 Plan for the unexpected
A lot can go wrong when shipping temperaturecontrolled goods, so consider all potential supply chain disruptions and associated costs. For example, if there’s a higher risk of a shipment getting held up in customs, you may want to use more expensive packaging that holds temperature longer or select a carrier that will re-ice a shipment if it is delayed.
10 Align with organizational green initiatives
Sustainability continues to be an important component in an organization’s decision-making, so make sure your cold chain operations align with your company’s sustainability goals. This may require finding alternatives to Styrofoam coolers or planning how to optimally return reuseable packaging.